Ice protection systems are designed to keep atmospheric ice from accumulating on aircraft flight surfaces while in flight. The effects of ice accretion on an aircraft can cause loss of control, resulting in a catastrophic flight event.
Types of ice protection systems
a) Pneumatic deicing boots
a) Pneumatic deicing boots
c) Electro-mechanical
i. Weeping Wing
ii. Electro-Mechanical Expulsion Deicing System (EMEDS)
iii. Hybrid Electro-Mechanical Expulsion Deicing System
The pneumatic boot is a rubber device attached to a wing's leading edge, invented by the Goodrich Corporation (previously known as B.F. Goodrich) in 1923. Portions of the boot are inflated to b
reak ice off the boot, de-icing the wing. Rubber boots are used on jets and propeller driven aircraft.
A bleed air system is used by jet aircraft to keep flight surfaces above the freezing temperature required for ice to accumulate (called anti-icing). The hot air is "bled" off the jet engine into tubes ro
uted through wings, tail surfaces, and engine inlets.
Electrical thermal systems use electricity to heat the protected surface. The electric heaters are usually flexible enough to use as anti-icers or de-icers. As a de-icer, the heater melts the ice, the ice no longer sticks to the surface due to aerodynamic forces. As an anti-icer, the heater keeps the surface to the point that the ice does not form.
Electro-mechanical Expulsion Deicing Systems use a mechanical force to knock the ic
e off the flight surface. Typically, actuators are installed underneath the skin of the structure. The actuator is moved to induce a shock wave in the protected surface to dislodge the ice.
Hybrid Electro-Mechanical Expulsion Deicing Systems combine an EMEDS de-icer with an electrical heating element anti-icer. The heater prevents ice accumulation on the leading edge of the airfoil and the actuators of the EMED system remove ice that accumulates aft of the heated portion of the airfoil.
A weeping wing system uses a liquid (such as ethylene glycol) to coat the surface and prevent ice from accumulating.
Airframe icing
i. Weeping Wing
ii. Electro-Mechanical Expulsion Deicing System (EMEDS)
iii. Hybrid Electro-Mechanical Expulsion Deicing System
The pneumatic boot is a rubber device attached to a wing's leading edge, invented by the Goodrich Corporation (previously known as B.F. Goodrich) in 1923. Portions of the boot are inflated to b

A bleed air system is used by jet aircraft to keep flight surfaces above the freezing temperature required for ice to accumulate (called anti-icing). The hot air is "bled" off the jet engine into tubes ro

Electrical thermal systems use electricity to heat the protected surface. The electric heaters are usually flexible enough to use as anti-icers or de-icers. As a de-icer, the heater melts the ice, the ice no longer sticks to the surface due to aerodynamic forces. As an anti-icer, the heater keeps the surface to the point that the ice does not form.
Electro-mechanical Expulsion Deicing Systems use a mechanical force to knock the ic

Hybrid Electro-Mechanical Expulsion Deicing Systems combine an EMEDS de-icer with an electrical heating element anti-icer. The heater prevents ice accumulation on the leading edge of the airfoil and the actuators of the EMED system remove ice that accumulates aft of the heated portion of the airfoil.
A weeping wing system uses a liquid (such as ethylene glycol) to coat the surface and prevent ice from accumulating.
Airframe icing
Ice accumulates on the leading edge of wings, tailplanes, and vertical stabilizers as an aircraft flies through a cloud containing super-cooled water droplets. Super-cooled water is water that is below freezing, but still a liquid. Normally, this water would turn to ice at 32 F, but there are no "contaminants" (droplet nuclei) on which the drops can freeze. When the airplane flies through the super-cooled water droplets, the plane becomes the droplet nucleus, allowing the water to freeze on the surface. This process is known as accretion.
A popular misconception is that aircraft icing events result from the weigh
t of accreted ice on the airframe. This is not the case. Rather, airframe icing causes problems by modifying the airflow over flight surfaces upon which the ice accretes. When ice accretes on aerodynamic lift surfaces, such as the wing and tailplane, the modification of airflow changes the aerodynamics of the surfaces by modifying both their shape and their surface roughness, typically increasing their drag and decreasing their lift. The particular effect of icing on the aerodynamics of a lift surface is a complicated function of the ice shape and location as well as of the amount of ice. These characteristics in turn depend in a complicated fashion on atmospheric conditions such as the amount, temperature, and droplet size of water in the air. The composite effect of this aerodynamic deterioration over all lift surfaces is a degradation of aircraft flight dynamics. In severe atmospheric conditions, dangerous levels of icing can be obtained in as little as 5 minutes. S
mall to moderate amounts of icing generally cause a reduction in aircraft performance in terms of climb rates, range, endurance, and maximum speed and acceleration. Icing effects of this type are known as performance events. As icing increases, separation of air flow from the flight surfaces can cause loss of pilot control and even wildly unstable behaviour. These more severe icing events, known as handling events, are often precipitated by a change in the aircraft configuration or an aircraft maneuver effected by a pilot unaware of the flight-dynamics degradation. This was the case with American Eagle Flight 4184 where the aircraft experienced an uncontrolled roll of 120 degrees in five seconds after the pilot initiated a flap retraction. Handling events generally can be classified into either tailplane stall, where the aircraft pitches forward, or asymmetric wing effects causing a roll upset (or roll snatch) as in the American Eagle Flight 4184 accident.
A popular misconception is that aircraft icing events result from the weigh

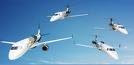
Rotary-surface icing
Ice can also accumulate on helicopter rotor blades and aircraft propellers. The accretion causes weight and aerodynamic imbalances that are amplified due to the rapid rotation of the propeller or rotor.
Engine-inlet icing
Ice accreting on the leading edge (lip) of engine inlets causes flow problems and can lead to ice ingestion. In turbofan engines, laminar airflow is required at the face of the fan. Because of this, most engine ice protection systems are anti-ice systems (prevent build up).